Entrepôt logistique
Comment résoudre concrètement les problèmes en entrepôt logistique que l’on peut rencontrer ? Voyons une démarche étape par étape, illustrée grâce à un exemple concret, type « sac de nœuds » bien connu du secteur. Il s’agit d’une expérience personnelle que je souhaite partager pour aider et peut être apporter des idées. Tel Sherlock Holmes, nous allons mener l’enquête.
Récapitulatif des étapes :
- Investiguer sur le terrain
- Analyser les données du SI
- Chercher les causes profondes
- Hiérarchiser les causes
- Trouver les solutions
- Mettre en place les solutions
- Suivre les indicateurs
L’alerte qui remonte de l’entrepôt
Exemple :
- « Il y a des manquants au picking. »
- « On perd du temps ! »
- « Ca plombe la prod !»
Nous sommes dans un entrepôt logistique Retail de préparation de commande pour des magasins. La prise se fait au picking avec des chariots double fourche. Le picking peut contenir une palette complète 80×120 ou différents types de meubles plus petits comme des tiroirs, des gravitaires simple et des casiers. Dans la suite, un « Cariste » conduit un chariot élévateur et effectue le réapprovisionnement du picking. Un « préparateur » utilise un chariot double fourche pour faire de la préparation de commande sur palette.
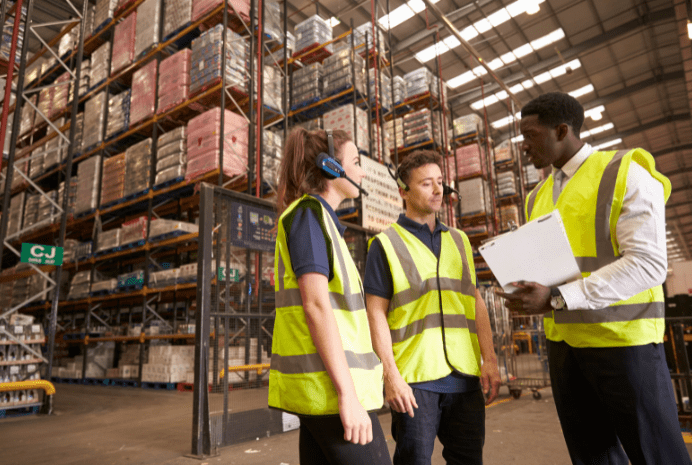
Résolution des problemes en entrepot
1 : Investiguer sur le terrain
La première étape pour résoudre un problème dans l’entrepôt est d’aller sur le terrain et de recueillir les témoignages des utilisateurs et manageurs. On va chercher des données concrètes sur la problématique, la fréquence, identifier si c’est un irritant qui arrive de temps en temps ou s’il y a une vraie perte de temps ou un risque. Cela permet de donner le niveau d’urgence et de moyens à mettre.
Exemple d’échange avec un préparateur :
Question : Quel est le problème ?
Réponse : Quand j’arrive pour prendre un colis, le picking est vide.
Question : Quelle est la fréquence ?
Réponse : Une fois ou 2 fois par palette préparée
Question : que faites-vous quand ça arrive ?
Réponse : Je déclare le manquant à la vocale puis je continue la préparation. Je reviens sur le picking en fin de préparation. Des fois je roule sur 3 à 4 cellules pour récupérer le manquant.
2 : Analyser les données du SI
La seconde étape est d’extraire les données du système informatique de gestion d’entrepôt (WMS). Le but est de chercher les preuves du problème et de vérifier la cohérence avec les informations récoltées sur le terrain.
Pour cela, il est nécessaire d’identifier un indicateur pertinent et de vérifier sa justesse. En effet on peut faire dire n’importe quoi aux données. Et, sans vérification de cohérence, il est possible de partir dans la mauvaise direction. Une fois que l’on a l’indicateur, il est judicieux de le convertir en « temps perdu » pour voir ce que ça représente en termes de temps ou d’argent.
Exemple d’analyse :
Pour trouver l’indicateur pertinent, on a cherché comment compter les manquants. Le plus simple est de constater le manquant sur le terrain, de relever l’heure, le picking, l’utilisateur, le numéro de support et regarder dans la base de données comment cela apparait. Une fois qu’on a trouvé l’indicateur, il est intéressant de monter des graphiques pour plus de visibilité. Enfin, trouver un ordre d’idée de temps perdu avec la distance moyenne entre la dernière prise d’une préparation, permet d’adapter les moyens que l’on va mettre en place pour résoudre le problème.
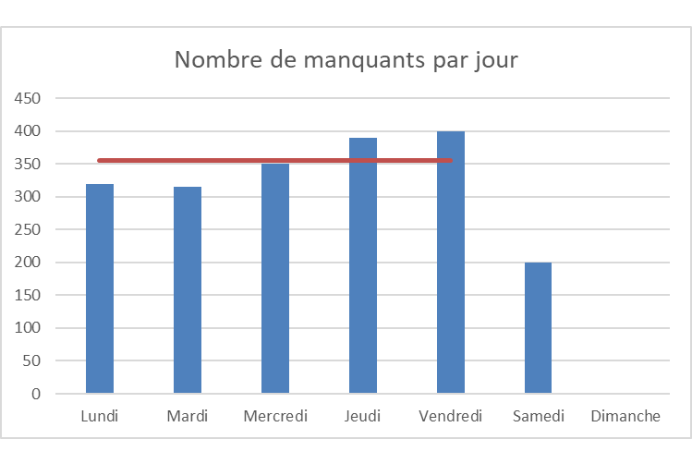
Vérification de cohérence : 355 manquants par jour correspond à 1,1 manquants par palette.
Avec 17h30 perdues par jour pour retourner chercher les manquants (2,5 ETP), c’est un sujet à prendre en considération.
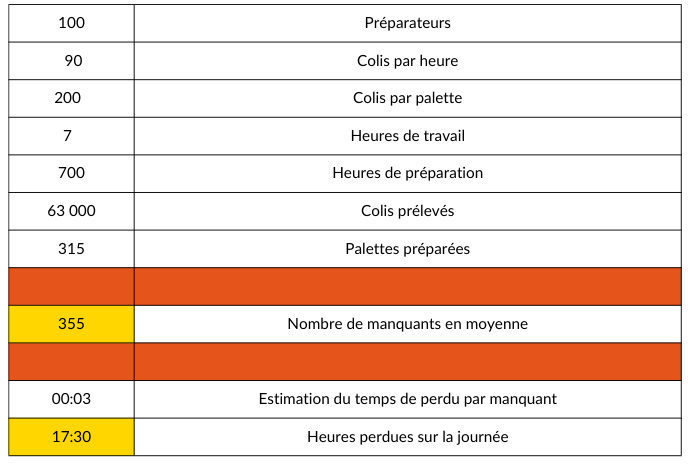
3 : Chercher les causes profondes
En s’appuyant sur l’analyse des données, sur le paramétrage du WMS ou sur l’avis des opérationnels, on va rechercher les causes, identifier le mobile. Le plus simple est de prendre des exemples concrets.
Il existe des méthodes connues et reconnues pour nous aider. Le QQOQCP (Quoi, Qui, Où, Quand, Comment, Pourquoi) donne l’occasion de mener une analyse fine et constructive de la situation. Ou encore, la méthode des « 5 pourquoi » permet de remonter aux causes profondes. Faire un brainstorming permet de réfléchir à plusieurs et faire émerger des idées originales et spontanées.
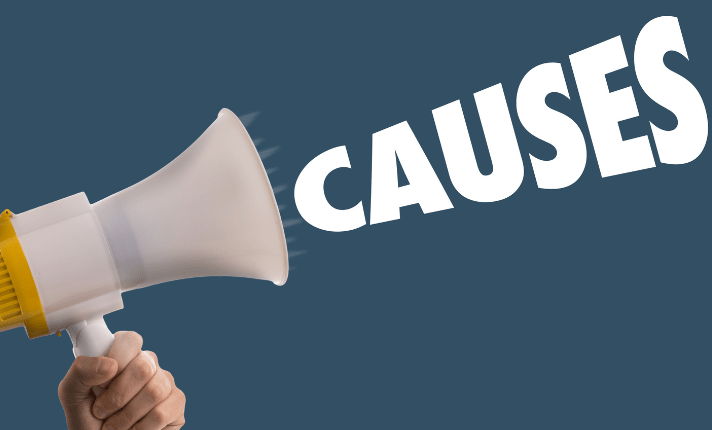
Exemple de causes :
Après avoir extrait la vingtaine d’emplacements générant le plus de manquants, une analyse de chacun des cas est faite. On décompose, dans le système et les process, ce qui peut expliquer que le produit n’est pas présent au picking quand le préparateur accoste. A l’issue des différentes méthodes présentées ci-dessus, et pas mal d’heures à se casser la tête, voici une liste des causes identifiées.
- Les caristes n’ont pas le temps de réapprovisionner avant l’arrivée des préparateurs. Au lancement de la préparation, les caristes partent en même temps que les préparateurs.
- Le nombre de caristes n’est pas adapté à la charge. 2300 réappros sont à faire par jour avec des variations pendant la journée. Le dimensionnement quotidien de 20 caristes à 15 réappros par heure en moyenne donne une capacité de 2100 réappros par jour.
- Certains caristes remplissent partiellement le picking. Un cariste met un colis alors qu’il peut en déposer 10.
- Des écarts de stock physique entre le WMS et la réalité sont présents. Dans le système il reste 2 colis, alors que, physiquement, il n’en reste aucun. Cela provient d’erreurs de prises qui peuvent être dues au conditionnement du produit. Le préparateur se trompe entre la prise au colis ou à l’unité.
- Le paramétrage du seuil de réappro n’est pas adapté. Le minimum picking est paramétré à 0 donc le réappro se déclenche quand le picking est vide. Le préparateur se présente avant que le réapprovisionnement se fasse.
- Le meuble n’est pas adapté à la consommation courante. Un produit est prélevé 200 fois par jour mais son picking ne peut en contenir que 20 parce que c’est un emplacement de meuble gravitaire. Le picking est réapprovisionné 10 fois dans la journée. Dans cette configuration, le picking est régulièrement vide et le travail du cariste n’est pas optimisé.
- Lors d’une promotion, la demande d’un produit explose du jour au lendemain. Un produit pris trois fois par semaine en temps normal est demandé 30 fois sur une journée.
4 : Hiérarchiser les causes
Une fois les causes trouvées, la pondération de chacune permet de prioriser le travail. On essaye de chiffrer les occurrences, de jauger l’importance du mobile. Cette étape se fait avec un responsable d’exploitation qui peut décider de prioriser une cause dont la solution est facile à mettre en place ou bien si elle est critique ou dangereuse. L’objectif est de hiérarchiser les causes pour avoir une vision d’ensemble et pour savoir dans quel ordre on va chercher et mettre en place les solutions. C’est étape est importante pour ne pas partir dans tous les sens.
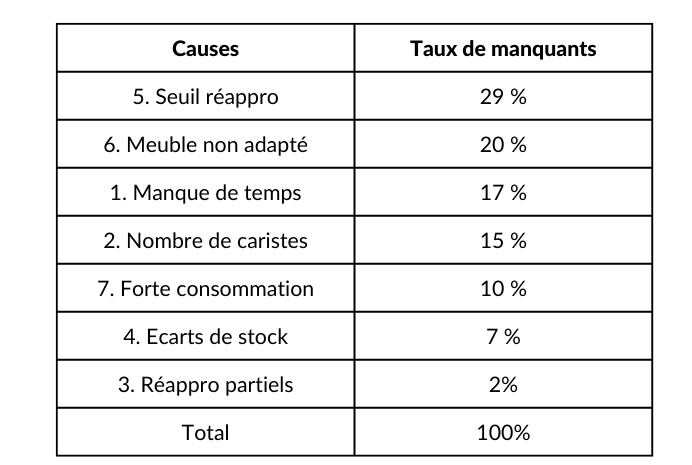
5 : Trouver des solutions
A cette étape, on va réfléchir aux solutions avec les équipes opérationnelles. Il est nécessaire d’intégrer les collaborateurs pour qu’ils donnent leurs idées, s’en imprègnent et se préparent au changement. C’est maintenant que l’on soupçonne le(s) coupable(s).
Il existe différentes façons de procéder :
- Soit aller voir un collaborateur particulier, expert dans son domaine, lui expliquer puis échanger sur une problématique qui le concerne.
- Soit le problème est transversal et une réunion avec un représentant de chaque équipe concernée est plus efficace.
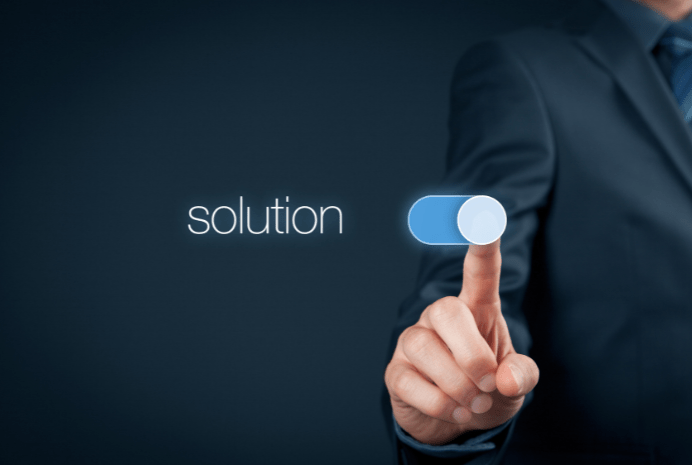
6 : Mettre en place les solutions
Une fois les solutions trouvées, un plan d’action est à mettre en place, pour faire « avouer le coupable ». Les solutions venant du terrain sont plus faciles à installer. Il est important de prendre le temps de former, d’expliquer et d’accompagner les utilisateurs. Imposer une solution toute prête, sans expliquer pourquoi, ça ne fonctionne pas.
7 : Suivre les indicateurs dans le temps
Tout au long du déploiement des solutions, le(s) indicateur(s) trouvé(s) lors de l’étape d’analyse de données sont surveillés. Cela permet de vérifier que le remède est efficace. On s’assure qu’il n’y a pas d’effet de bord. En cas de dégradation de l’indicateur, il faut alerter et relancer. Les progrès peuvent prendre du temps en fonction de la cause et de l’inertie de l’entrepôt. Mais si de bonnes bases sont posées, le bénéfice sera encré sur le long terme.
Exemple : tableau récapitulatif
Pour plus de lisibilité de l’exemple de cet article, voici un tableau récapitulatif des solutions et de leurs mises en place.
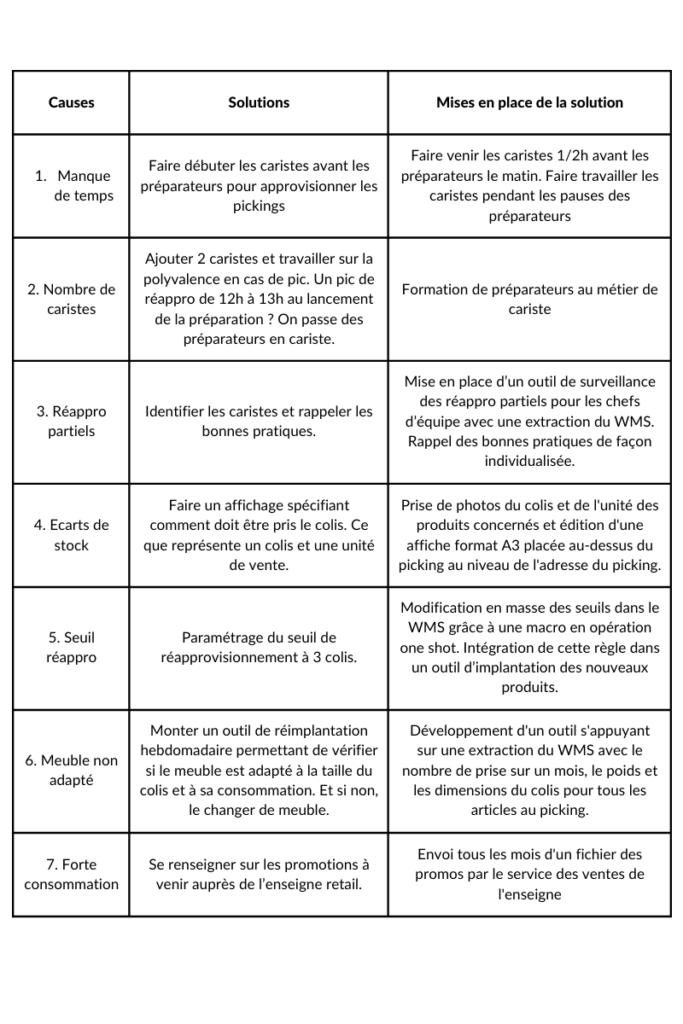
Conclusion
Comme une enquête, résoudre des problèmes, c’est découvrir le(s) coupable(s). En se renseignant, examinant, fouillant, s’informant, cherchant, en s’appuyant sur des faits et des rapports objectifs, on va démêler la pelote et trouver qui a assassiné le picking dans l’allée D55.
Cet article n’a pas pour but de donner des solutions toutes faites à des professionnels aguerris mais plutôt de donner des pistes et, pourquoi pas, d’emmener des détectives vers les métiers de la Supply Chain.
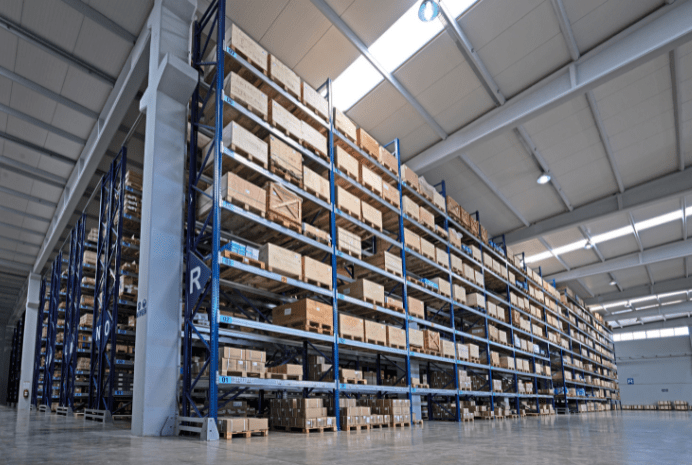
A propos de l'auteure
Eliane Consola est consultante / cheffe de projet SI Supply Chain au sein du cabinet CHRYMELIE et apporte sa connaissance des systèmes d’information logistique auprès de nos clients. Tel un cocher assertif, elle guide les équipes opérationnelles et informatiques pour mener le projet sur le chemin de la réussite.