Industrie 4.0
L'origine de cette nouvelle stratégie
Dans les années 80, l’industrie manufacturière connait une révolution importante avec la démocratisation de l’automatisme et la robotisation. Cette révolution est comparable à ce qu’a vécu l’industrie financière durant sa longue transformation digitale.
Alors que les volumes de production s’accroissent, le contrôle est omniprésent à l’intérieur de chaque processus / moyen de production. Les métiers et les besoins pour tendre vers l’excellence opérationnelle ont également évolués.
Les opérateurs de lignes ayant leurs taches simplifiées, des exemples montrent que leur carrière s’oriente vers le contrôle de qualité ou la gestion de production.
De nouveaux emplois apparaissent, souvent délégués à des intégrateurs, comme l’automaticien ou le programmeur de robot, permettant à l’entreprise de se focaliser sur son cœur de métier. Les emplois proches de la connaissance métier restent donc inchangés et sont d’autant plus valorisés que la productivité augmente.
Plus les cadences s’accélèrent, plus les engagements de délai sont stricts et plus les arrêts coûtent cher à l’ensemble de la chaîne des fournisseurs.
Devant cette nouvelle criticité des moyens de productions, alors que les ressources humaines restent globalement identiques, de nouveaux challenges apparaissent.
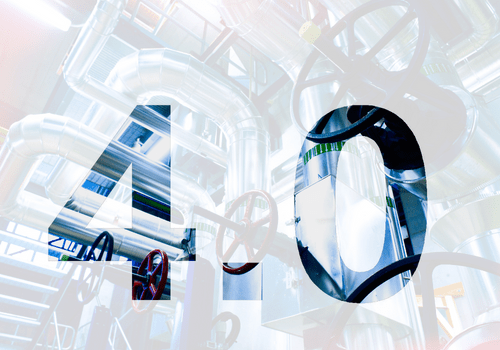
La maîtrise de l'information
L’information est la clé pour comprendre le passé, voir le présent, réagir, et anticiper le futur dans le but d’atteindre l’excellence opérationnelle pour un coût optimal. Une usine manufacturière génère de nombreuses données prêtes à être transformées en information qui sera par la suite observée, analysée, mise en relation, puis utilisée dans des modèles d’aide à la décision.
L’industrie aujourd’hui bénéficie de toute l’expérience acquise dans les centres de données internationaux (Connectivité). Elle bénéficie également de toutes les avancées modernes en terme de Science des données, autrement appelées les domaines de l’Intelligence Artificielle (Réseau Neuronal, Machine Learning).
Technologies
L'industrie 4.0
L’industrie 4.0 regroupe toutes les technologies permettant l’extraction simple et la centralisation des données de production par l’implémentation d’un ensemble d’outils qui compose ce qu’on appelle le Système de Contrôle et d’Acquisition de Données (SCADA).
Elle supprime les tâches manuelles de suivi, améliore la précision et renforce les indicateurs.
Elle permet d’observer des données dans le temps, graphiquement, pour mieux détecter et comprendre les déviations d’un ou plusieurs moyens de production.
Les diagnostics sont alors simplifiés et les arrêts non-planifiés sont plus courts.
Le Contrôle de Qualité bénéficie d’un système de surveillance en temps réel et d’un historique de traçabilité à long-terme.
Basée sur le concept informatique appelé DIKW (Données, Information, Connaissance, Sagesse) ainsi que sur les bonnes pratiques de Data Management et de Sécurité Informatique, l’industrie 4.0 crée le socle nécessaire pour construire des projets à forte valeur ajoutée.
Digitalisation
La digitalisation des processus
Dans une unité de production manufacturière, les ingénieurs, mécaniciens et les techniciens de maintenance commencent à renseigner précisément leurs interventions. Il en découle un suivi automatique du stock de maintenance (MRO) et des temps moyens entre les failles (MTBF).
Le système d’apprentissage automatique (Machine Learning) peut alors détecter des opérations périodiques et proposer un planning d’interventions anticipées. L’anticipation est très importante en mécanique.
Elle évite les casses de matériel (gestion de stock de pièces de remplacement et délais fournisseurs) ainsi que les opérations de maintenance non-planifiées souvent plus chronophages que les interventions périodiques planifiées.
Le Taux de Fonctionnement brut est donc amélioré et, avec lui, le Taux de Rendement Synthétique (TRS).
La connectivité de l'entreprise avec le monde extérieur
Elle permet par exemple au client d’influer directement sur les moyens de production (personnalisation des produits et son conditionnement) et offre une traçabilité directe. La transparence et l’excellence renforcent la confiance dans la chaîne des clients/fournisseurs.
L'accueil de ces changements fondamentaux parmi les équipes
Les initiatives 4.0 sont bien accueillies par les équipes car elles sont une aide importante à leurs activités quotidiennes et un gain de temps significatif. L’objectif premier est de faire plus avec les ressources humaines existantes.
L’industrie 4.0 est un ensemble d’outils puissants de productivité pour l’Homme.
Au niveau de l’exécution :
Une information enrichie obtenue plus tôt permet une meilleure réactivité.
Les tâches à accomplir sont accélérées.
Exemple de projet
Mise en place d’un tableau de bord central avec des indicateurs de diagnostic en live sur les différents moyens de productions.
Mise en place d’alertes rangées directement dans l’ordre de priorité (qui peut être dynamique dans le temps) pour les interventions des techniciens, en fonction de la criticité des lignes, des produits, ou des livraisons Just-In-Time.
Génération automatique d’un plan de maintenance journalier, avec suggestions d’achat de matériel en fonction des cycles et délais fournisseurs observés.
– Au niveau du management :
Une information mesurée, tangible sur les performances permet une meilleure clarté et facilite la prise de décision.
On peut ainsi définir des objectifs, mesurer l’impact et la progression des améliorations.
Les équipes voient en direct avec le management, leur progression positive.
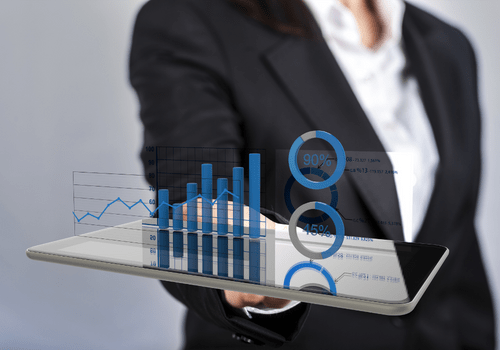
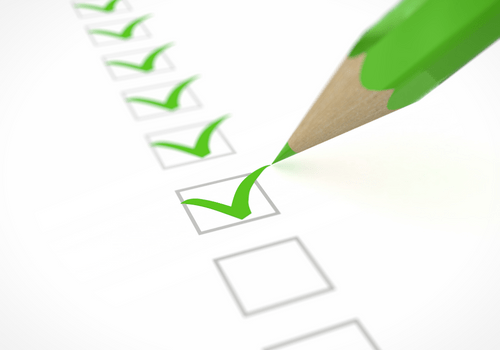
Exemple de projet
Définition précise des critères de satisfaction internes de rentabilité basés sur les outils de mesures mis à disposition dans le cadre des initiatives 4.0 (SCADA, mentionné précédemment).
Mise en place d’un tableau de bord central avec les indicateurs de performance en live sur les différents moyens de productions, permettant l’observation des résultats, la sanction positive instantanée des équipes et la quantification précise de l’effort restant à fournir pour atteindre l’excellence.
Mise en place de rapports automatiques journaliers sur les incidents de l’ensemble des moyens de productions permettant de détecter les améliorations nécessaires au sein de l’organisation.
– Au niveau du travail d’équipe :
Une information partagée, pertinente, persistante, informatisée permet une meilleure collaboration.
La mémoire collective est renforcée et permet la progression par l’expérience indépendamment du turnover. Une dynamique communautaire se créer entre les différents corps de métier autour des sujets structurants (projet client, produit particulier).
Exemple de projet
Mise en place d’une plateforme sociale d’échange interne / communautaire organisée autour des produits et projets de l’entreprise. On y dépose les informations structurées nécessaires à la vie de l’entreprise, dans un modèle de données unique et central.
Mise en place d’un système de notes rapides et demande d’intervention par station ou zone d’atelier, gérées par un système de QR-code (code barre en 2 dimensions). Chaque zone a son responsable. Une liste publique de tâches à accomplir se génère et permet de voir l’avancement des demandes. Des coûts de maintenance relatifs à ces stations ou zones d’atelier sont par la suite directement observables, et des solutions plus économiques peuvent être identifiées, sans effort de mémorisation collective.
– Au niveau de la direction :
Les informations traitées automatiquement permettent une meilleure scalabilité et une meilleure flexibilité.
Le maintien d’indicateurs complexes et la gestion qui en découlent ne demande pas un effort exponentiel (temps/argent) par rapport au volume d’activité.
Les processus assistés par ordinateur permettent une croissance stable face à une multiplication des projets et des moyens de production.
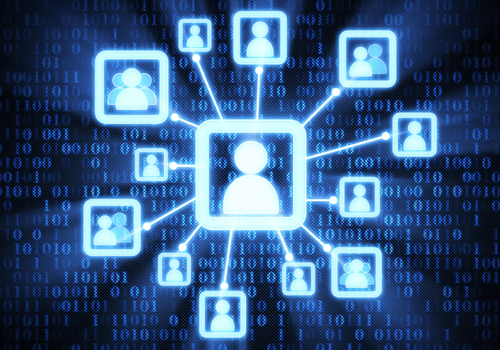
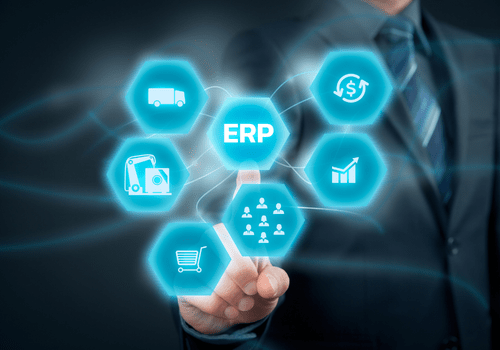
Exemple de projet
Intégration des processus gérés sous ERP (commandes, achats, comptabilité, stocks) avec les données en live de l’activité de l’entreprise (RFID, QR-code, capteurs de productions).
La définition de règles de prise de décision permettant au système de générer des suggestions basées sur l’expérience acquise, à valider lors des comités de direction.
Conclusion
Pour les PME et Grandes Entreprises, les initiatives 4.0 sont d’excellents moyens d’améliorer la rentabilité des centres de production en agissant à tous les niveaux grâce à une synergie entre les Hommes et la technologie.
Ces progrès sont rendus possibles par les connaissances et l’expérience acquises dans les domaines où l’informatique est un outil central incontournable.
A titre indicatif, pour une entreprise de 70 personnes avec des moyens de productions et un suivi conventionnel, l’implémentation d’un système d’acquisition de type SCADA simple, libère un temps équivalent à 3 personnes pour un investissement marginal. (ROI d’environ 6 mois en fonction du bassin d’emploi et de la maturité organisationnelle).
Un système SCADA intégré et plus complexe, permet la réduction des temps de maintenance d’au moins 20% sur l’exercice cyclique calendaire de référence. Il a été observé jusqu’à 50% d’amélioration sur les temps d’arrêts en périodes sensibles (effectif réduit ou cycles nocturnes générateurs d’erreurs opérationnelles à fort impact).
Nous publierons des études de cas dans les prochaines semaines et nous expliquerons comment sélectionner les compétences requises pour se lancer dans ces projets.
A propos de l'auteur
Philippe Fernandes est Ingénieur en industrialisation orienté Systèmes d’Information et Industrie 4.0 au sein du groupe français AdduXi, leader en injection plastique de précision dans l’industrie Automobile.
La société AdduXi et CHRYMELIE travaillent en partenariat sur la mise en œuvre de stratégies de digitalisation 4.0.
Lien connexes :
- Industrie 4.0
- Système SCADA
- Méthode Pyramide DIKW en Anglais
- Méthode Pyramide DIKW en Français
- Machine Learning
- Analyse par Réseau de Neurone
- Maintien en Conditions Opérationnelles
- Maintenance Prédictive
- Temps Moyen entre les pannes (MTBF)
- Taux de Rendement Synthétique
- AdduXi Injection plastique de précision
- CHRYMELIE : Conseil en Supply-Chain, Digital et Industrie 4.0